SMED là gì
Đây là phương pháp đã giúp Toyota thay đổi quy trình làm việc của máy dập 1000 tấn với thời gian làm việc trong 4 tiếng xuống chỉ còn 3 phút. SMED chính là một trong những chìa khóa chính để giúp các doanh nghiệp theo đuổi sản xuất tinh gọn đạt được một quy trình sản xuất tối ưu nhất. Cùng tìm hiểu về SMED là gì từ A đến Z qua bài viết sau.
1. SMED là gì?
SMED (Chuyển đổi nhanh) viết tắt là Single Minute Exchange of Dies có nghĩa là giảm thời gian chuyển đổi xuống số phút chỉ còn một con số.
Tuy nhiên, cụm từ “Single Minute” không có ý nghĩa là tất cả các chuyển đổi chỉ mất một phút, mà ý nghĩa của cụm từ này là sẽ mất ít hơn 10 phút (nói cách khác là “phút có một chữ số”). Từ “Dies” đề cập đến các công cụ chuyên dụng trong ngành sản xuất (ví dụ như cắt, tạo hình… có sử dụng máy ép) cần được sửa đổi và thiết lập lại khi mô hình sản xuất thay đổi.
Những thay đổi này có thể làm dừng quy trình trong một khoảng thời gian dài mà không tạo ra giá trị cho doanh nghiệp. Khoảng thời gian này có thể được cải thiện thông qua SMED.
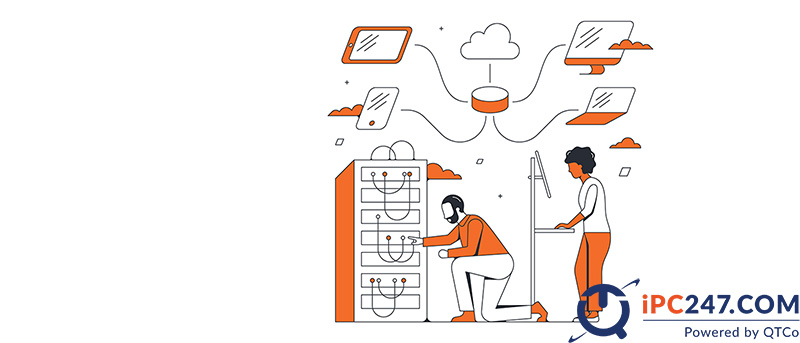
Thuật ngữ này còn được biết đến với tên gọi khác là QCO (Quick Changeover). Cơ bản, đây là phương pháp giúp giảm thời gian chuyển đổi (changeover time) giữa các loại sản phẩm trong quá trình sản xuất. Changeover time (thời gian chuyển đổi) được hiểu là thời gian cần thiết để chuyển đổi máy móc, dây chuyền từ sản xuất sản phẩm tốt này sang sản xuất sản phẩm tốt tiếp theo. Ban đầu, mục tiêu của việc thiết lập SMED là giảm thời gian cài đặt máy móc (setup) xuống dưới 10 phút. Tuy nhiên, ngày nay, phương pháp này được sử dụng để cải thiện mọi hoạt động liên quan đến “thiết lập quy trình”..

SMED được phát triển bởi Shigeo Shingo, một kỹ sư công nghiệp người Nhật Bản. Ông đã thành công đáng kể trong việc giúp các công ty sản xuất của Nhật Bản giảm thời gian chuyển đổi lên đến 94% (ví dụ: từ 90 phút xuống còn 50 phút). SMED đã trở thành một phần thiết yếu của sản xuất tinh gọn LEAN Manufacturing, giúp giảm lãng phí, tăng năng suất và tối ưu hóa chi phí.
2. Nguyên tắc hoạt động của SMED
Trong SMED, chuyển đổi nhanh được hình thành từ các thao tác bên trong và các yếu tố bên ngoài.
- Các thao tác bên trong: Đây là các thao tác bắt buộc mà doanh nghiệp phải thực hiện khi thiết bị ngừng hoạt động.
- Các yếu tố bên ngoài: Đây là các hoạt động mà doanh nghiệp có thể thực hiện và ảnh hưởng trong quá trình máy đang hoạt động.

SMED không yêu cầu đầu tư thêm nguồn lực để thực hiện chuyển đổi nhanh. Thay vào đó, nó tập trung vào biến quá trình chuyển đổi thành nhiều bước chuyển đổi bên ngoài, đồng thời đơn giản hóa và sắp xếp các bước còn lại, nhằm giảm tổng thời gian thực hiện (Lead Time).
3. Lý do doanh nghiệp sản xuất cần triển khai SMED
Các doanh nghiệp thường mắc phải vấn đề thời gian sản xuất kéo dài hơn yêu cầu thực của khách hàng. Một lý do phổ biến là do trong quá trình sản xuất, thời gian chuyển đổi giữa các loại hàng hóa khác nhau mất rất nhiều thời gian. Điều này tạo ra khoảng thời gian không sản xuất gọi là “khoảng thời gian chết”, gây lãng phí cho doanh nghiệp.
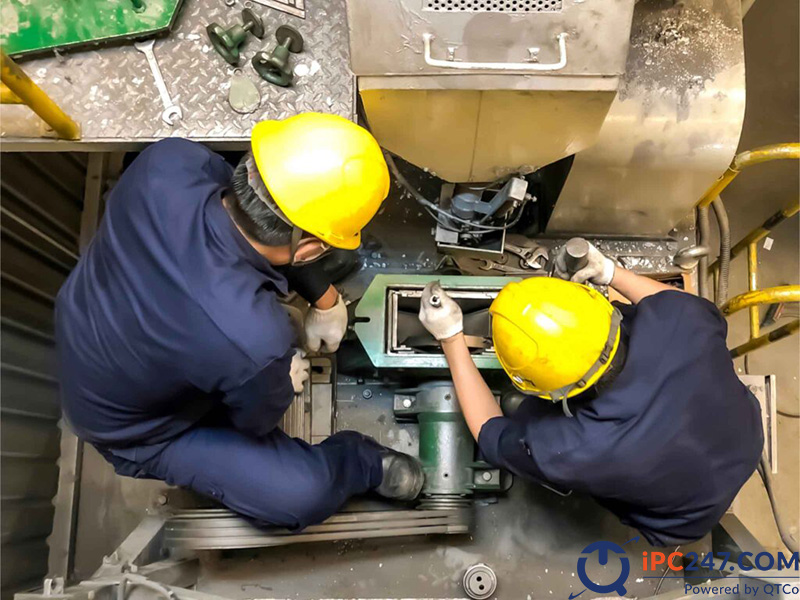
Vì vậy, việc sản xuất hàng loạt thường được lựa chọn để đạt được lợi thế kinh tế theo quy mô. Lợi ích kinh tế của sản xuất hàng loạt được tính bằng tỷ lệ giữa thời gian thực tế của quá trình sản xuất và thời gian chuyển đổi. Do đó, việc giảm thời gian chuyển đổi một cách hiệu quả sẽ giúp giảm thời gian sản xuất thực tế, từ đó đảm bảo rằng sản phẩm được giao đến khách hàng nhanh chóng hơn.
3. Lợi ích của SMED
Giảm chi phí sản xuất: Thời gian chuyển đổi nhanh hơn đồng nghĩa với thời gian máy móc – thiết bị không hoạt động ít hơn, từ đó giảm chi phí.
Kích thước lô nhỏ hơn: Thời gian chuyển đổi nhanh hơn cho phép thay đổi đơn vị sản phẩm thường xuyên hơn, giúp tăng tính linh hoạt trong lập kế hoạch sản xuất.

Cải thiện khả năng đáp ứng nhu cầu của khách hàng: Nhờ kích thước lô nhỏ hơn, việc lên lịch sản xuất linh hoạt hơn khi có thay đổi từ khách hàng, giúp đáp ứng nhu cầu của họ một cách tốt hơn.
Giảm tồn kho: Kích thước lô nhỏ hơn dẫn đến giảm tồn kho, giúp tiết kiệm không gian và tài nguyên của doanh nghiệp.
Khởi động mượt mà hơn: Quy trình chuyển đổi tiêu chuẩn hóa giúp cải thiện tính nhất quán và chất lượng sản phẩm, từ đó tạo ra sự khởi động suôn sẻ hơn.
Giảm số lượng sản phẩm chưa hoàn thiện (WIP): Thời gian chuyển đổi nhanh hơn giúp giảm số lượng sản phẩm chưa hoàn thiện trong quá trình sản xuất.
Nâng cao năng suất trên dây chuyền: Thời gian chuyển đổi nhanh hơn giúp tăng năng suất của dây chuyền sản xuất.
Tăng khả năng sinh lợi (ROI) từ thiết bị sản xuất cho doanh nghiệp.
4. 6 bước triển khai thực hiệm SMED
Bước 1 – Quan sát tình trạng hiện tại và đo đạc thời gian chuyển đổi
Đầu tiên, quá trình SMED thường bắt đầu bằng việc quan sát tình trạng hiện tại và ghi lại quy trình trong một đoạn video. Điều này rất quan trọng để hiểu rõ các vấn đề mà doanh nghiệp đang gặp phải và xác định mức độ cải tiến cần thực hiện.
Trong quá trình này, người phân tích cần chú ý đến cả yếu tố “con người” (người vận hành) và yếu tố “thiết bị” (máy móc – thiết bị vận hành).
Bạn có thể tạo một bảng theo dõi đơn giản để điều tra quá trình thiết lập/chuyển đổi (bao gồm: mô tả hoạt động, thời gian hoạt động, thời gian sửa chữa hoạt động, loại hoạt động – nội bộ hoặc bên ngoài).
Hơn nữa, bạn nên đo đạc thời gian chuyển đổi nhiều lần, vì các người khác nhau có thể thực hiện theo cách khác nhau, sau đó sử dụng thời gian chuyển đổi trung bình giữa các lần đo.
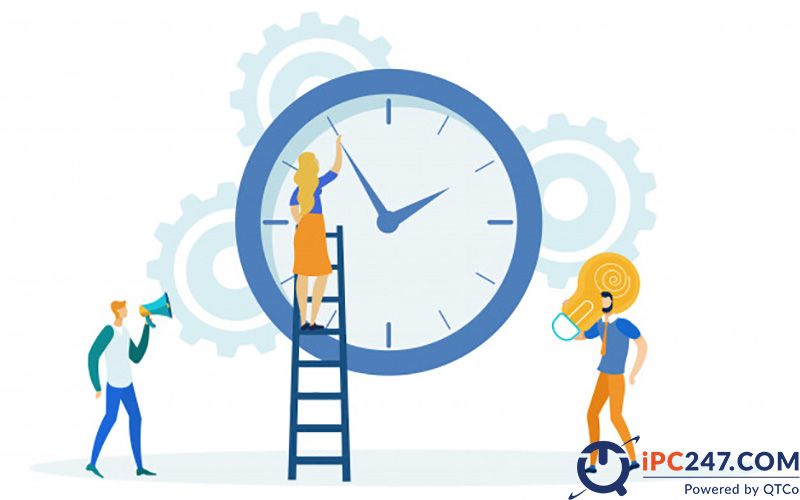
Bước 2 – Xác định các thao tác bên trong và bên ngoài
Ở bước này, bạn cần xác định các thao tác có thể thực hiện khi máy đang hoạt động và các thao tác được thực hiện khi máy phải dừng. Sau đó, phân loại chúng theo màu sắc để quản lý cho các bước tiếp theo.

Bước 3 – Phân tách các thao tác bên ngoài
Tiếp theo, bạn có thể chuyển các thao tác bên trong thành các thao tác bên ngoài càng nhiều càng tốt, nhằm mục đích loại bỏ các lãng phí như tìm kiếm, thao tác, vận chuyển… Phân tích tình huống, đánh giá hoạt động và xác định cơ hội chuyển đổi từ “bên trong” sang “bên ngoài”.
Bước 4 – Sắp xếp và cải tiến các thao tác bên trong
Sau khi chuyển các thao tác bên trong sang bên ngoài, doanh nghiệp cần rút ngắn thời gian của các thao tác bên trong để giảm thiểu thời gian dừng. Bước này được thực hiện dựa trên các nguyên tắc sau: không chọn lựa, không tìm kiếm, không di chuyển qua lại. Khi thực hiện các hoạt động “bên trong”, doanh nghiệp cần xác định các thao tác/công việc có thể hoàn thành cùng một lúc hoặc đồng thời.
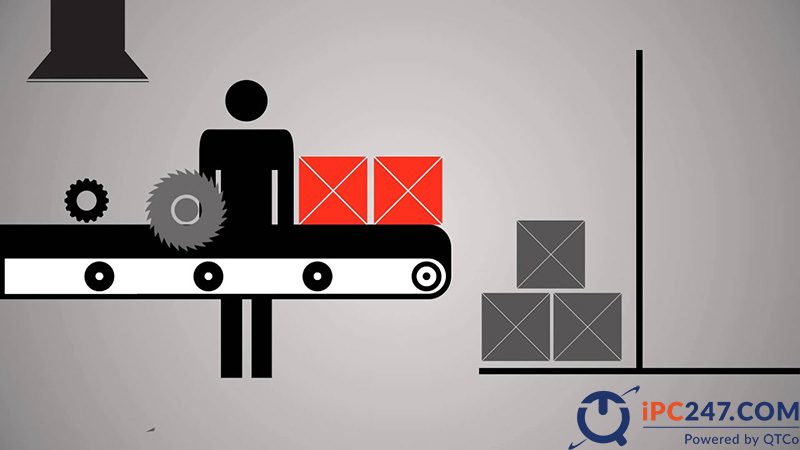
Sau đó, đưa ra tổng kết, phân tích, đánh giá và dự đoán kết quả. Việc thực hiện chuyển đổi nhanh có thể được kết hợp với quy trình 5S và các hoạt động quản lý trực quan khác.
Bước 5 – Sắp xếp và cải tiến các thao tác bên ngoài
Bước tiếp theo là nghiên cứu phương pháp để giảm thời gian các thao tác chuyển đổi bên ngoài. Mặc dù các thao tác bên ngoài không góp phần trực tiếp vào việc giảm thời gian dừng trong quá trình chuyển đổi, nhưng chúng đóng vai trò quan trọng trong việc giúp rút ngắn thời gian các thao tác bên trong. Điều này giúp giảm thời gian tổng thể của quá trình và giảm khối lượng công việc cho công nhân.

Bước 6 – Chuẩn hóa quy trình và duy trì quy trình mới
Đây là bước chuẩn bị cần thiết để sẵn sàng cho việc thực hiện cải tiến. Bộ phận thực hiện chuyển đổi nhanh cần xác định: ai sẽ làm gì, vị trí của dụng cụ – vật tư – máy móc, những người tham gia, bảng hướng dẫn chi tiết triển khai công việc một cách hiệu quả…

Cần cụ thể hóa các ý tưởng cải tiến cho các công việc, lập bảng kiểm tra chuyển đổi nhanh và văn bản hóa các tiêu chuẩn mới. Việc áp dụng SMED một lần không đủ. Bạn cần thực hiện nó liên tục và đào tạo cho công nhân về những tiêu chuẩn mới. Nếu không duy trì, bất kỳ tiêu chuẩn nào được thiết lập cũng sẽ nhanh chóng bị lãng quên.
Đây là phương pháp đã giúp Toyota thay đổi quy trình làm việc của máy dập 1000 tấn với thời gian làm việc trong 4 tiếng xuống chỉ còn 3 phút. SMED chính là một trong những chìa khóa chính để giúp các doanh nghiệp theo đuổi sản xuất tinh gọn đạt được một quy [...] Xem bài viết chi tiết tại: https://ipc247.com/smed-la-gi/
Comments
Post a Comment